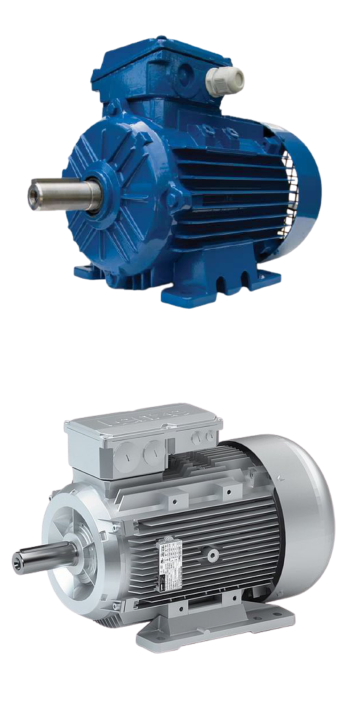
The AC induction motor is an electro-mechanical device. The fundamental operation of an AC motor relies on the principles of magnetism. It is made up of two major components: the stationary stator (lamination and copper windings) that is on the outside and the inside rotor that is laminations/aluminum attached to the output shaft.
When an electric (AC) charge is applied to the coil of wire, it becomes an electromagnet, generating a magnetic field. Simply described, the laminations provide enough angular offset between the field and rotors creating motion. The shaft then begins to rotate, operating the motor.
The mechanical motion comes from utilizing the force that is exerted by the rotating magnetic fields produced in the stator by the alternating current that flows through its coils. As such they are synchronized to frequency, a fixed speed. It is universally accepted that the internal configuration of laminations and coils allows these motors to run at specific speeds, so most people will know that a 2 pole AC motor operates at 3600 RPM and a 4 pole AC motor at 1800 RPM.
Many speed variations are available so please, check with our sales team for speed options. Since these types of motors do not contain magnets or complex controllers for operation it makes them very economical to manufacture resulting in a low purchase price. In higher horsepower applications, the AC induction motor is one of
the most efficient motors in existence. Another one of the advantages of AC motors is the incredibly smooth operation they can provide as a result of low torque ripple.
If a variable speed motor option is required or desired, a three phase AC motor can be used with a variable frequency drive (VFD). By simply varying the voltage and frequency of the applied waveform using a VFD the motor speed and torque can be controlled. These types of motors are commonly available, and with VFD’s to control speed, they are economical to use.
If you would like us to prepare a competitive quote on AC motors, please contact our sales team.